The Chewy Autonomous Mobile Picking (CHAMP) Challenge
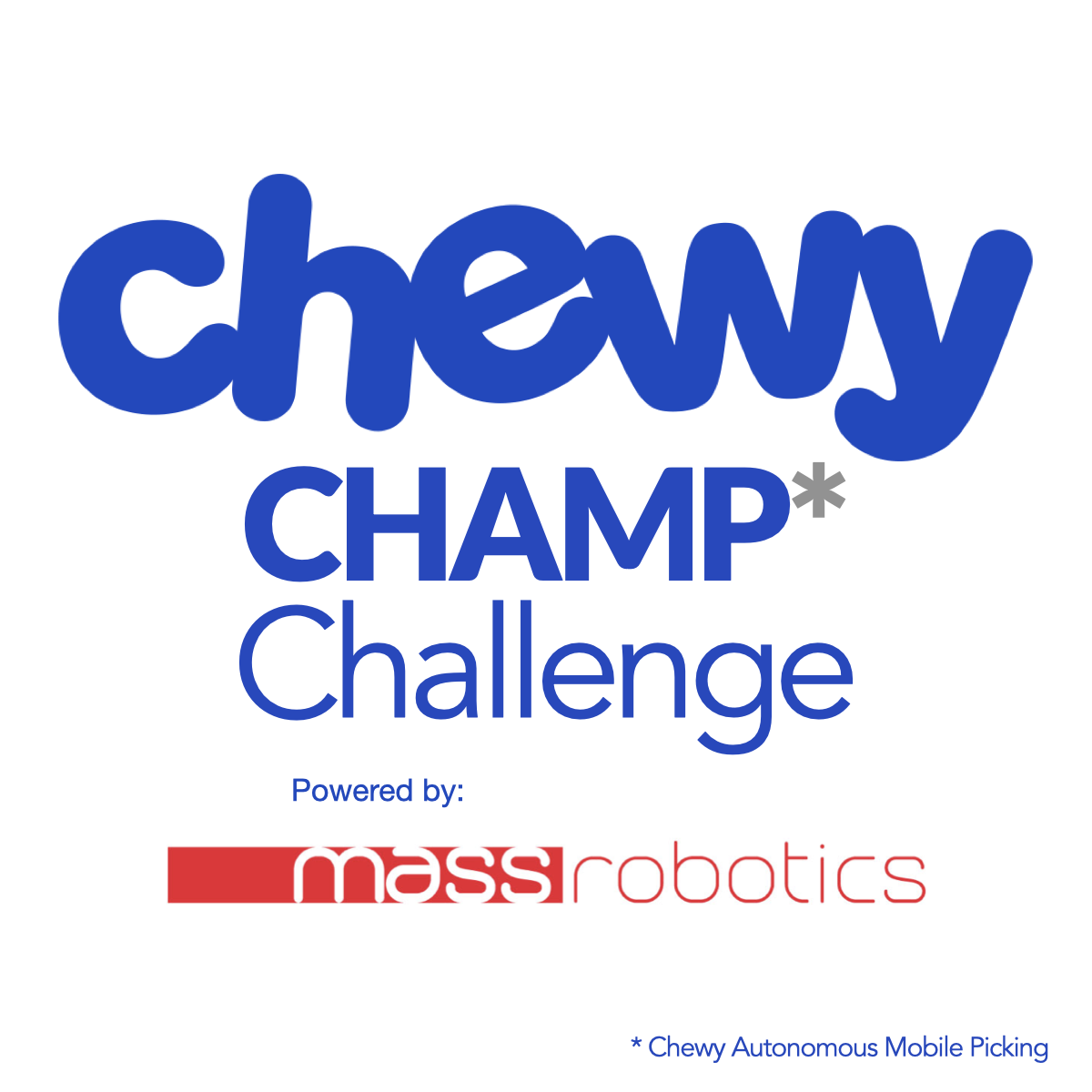
What is the CHAMP Challenge?
The CHAMP Challenge is designed to solve a critical issue in modern warehousing: how to automate the handling of large, heavy, and awkwardly shaped items in confined spaces. Handling sacks, boxes, and pails of products like dog food and cat litter is physically demanding and difficult to automate, particularly because robotic systems struggle to securely grip and manipulate these items. This challenge is amplified in environments like Chewy’s warehouses, where space is often limited, and robots must work alongside humans, prioritizing both efficiency and safety.
Read more >>
The Problem
As an e-commerce retailer, Chewy processes millions of orders per week, many involving large or heavy products. Manually picking and packing these items increases the risk of workplace injuries and limits operational efficiency. In confined warehouse spaces, introducing robotic arms to grip and manipulate variously shaped sacks and pails requires advanced AI and robotics solutions. The complexity of securely grasping, lifting, and placing these items into open cardboard boxes—without damaging the items or disrupting the workflow—poses a significant engineering challenge.
Beyond just the physical task, the solution must seamlessly integrate with human workers, supporting their labor and ensuring safety while enhancing productivity. In the broader context of the robotics and automation industry, solving this problem pushes forward the capabilities of collaborative robots, offering practical solutions that benefit both human workers and overall warehouse operations.
Chewy’s Interest
Chewy is deeply invested in addressing this issue, as it directly impacts the efficiency and safety of its warehouse operations. By automating these difficult picking tasks, Chewy aims to improve operational throughput, reduce the risk of worker injuries, and create a safer, more efficient working environment. Additionally, this challenge aligns with Chewy’s long-term vision of leveraging robotics and automation to enhance its logistics and e-commerce capabilities.
By tackling this challenge, participants will contribute to the advancement of warehouse automation, helping to drive the industry forward while solving a real-world problem for Chewy. The winning solution will not only demonstrate technical innovation but will also showcase the potential for scalability and integration into Chewy’s existing operations.
Technology we are looking for:
Challenge benefits :
- Grasp and lift various items, including sacks, boxes, and pails of dog food and cat litter, from standard pallets.
- Efficiently place these items into open cardboard boxes with precision, ensuring stability and maximizing space utilization.
- Operate in confined warehouse environments while working safely alongside human employees.
- Incorporate AI-driven decision-making, including reinforcement learning, to adapt to different handling conditions and improve over time.
- First Place: $30,000 cash prize.
- Collaboration Opportunity: The winning team will have the chance to enter into a contract with Chewy to further develop the proposed solution.
- Recognition: The winning team will be recognized at a MassRobotics event, providing exposure to industry leaders and potential partners.
timeline:

FAQS
What does the robot solution need to do?
Applicants must design a fully autonomous robot solution capable of:
- Grasping and Lifting: Handling various objects, including bags, boxes, and pails of dog food and cat litter.
- Handling Conditions: The robot must pick items from stacks on standard pallets (40″x48″), with a maximum stack height of 60″.
- Grasping Mechanism: The robot should use advanced gripping techniques such as adaptive grippers or vacuum-based systems to securely handle items of different shapes and weights.
- Placement: The robot must place these items into open cardboard boxes with open flaps.
- Accuracy and Efficiency: Placement must be precise to maximize space use and ensure the stability of packed items.
- Fallback Mechanisms: Easy error recovery methods must be implemented to assist facility workers in case of failures.
What are the payload and dimension requirements?
- Minimum Payload: 10 lbs.
- Maximum Payload: 60 lbs.
- Item Dimensions:
- Minimum: 6″x6″x6″ (LWH)
- Maximum: 30″x20″x20″ (LWH)
What characteristics should the robot solution have?
- Collaboration: The robot must be collaborative and designed to safely operate alongside human workers.
- Autonomy: The robot must be fully autonomous, using AI for decision-making in tasks such as path planning, object recognition, and manipulation.
- Reinforcement Learning: The robot should integrate reinforcement learning to improve performance over time by learning from its environment and tasks.
- Integration: The design and simulation must be compatible with the Nvidia Omniverse platform for training and testing.
- Height Limitation: The robot’s total height must not exceed 7 feet to fit within standard warehouse environments.
Are there any specific technical notes or constraints?
- Vision System: Cameras can be mounted over fixed pick and place points, and item-level recognition is not required. Chewy can provide pick-and-place point training data if necessary.
- AMR Portion: Solutions can either use an AMR or creatively bypass the need for one entirely.
- Item Recognition: Assume that all items on the pallet are uniform, eliminating the need for individual item recognition.
- Pallet Condition: Items will be securely stacked on pallets without shrink wrap.
- Sample Items: Chewy will provide sample items to represent the minimum-to-maximum threshold of handling (MTBH) ranges for testing and validation.
What is the evaluation process?
- Phase 1 Criteria:
- Track Record & Experience: Evaluation of the applicant’s background and previous work.
- Innovation & Design: Creativity and ingenuity in the proposed robot design.
- Functionality & Scalability: The ability of the solution to meet the specified requirements and potential for scalability.
- Phase 2 Criteria:
- Efficiency & Accuracy: Speed and accuracy in handling and placing items.
- Scalability: The solution’s potential for commercial use and integration into real-world operations.
If you have any other questions, please contact us below.
- MassRobotics: info@massrobotics.org
Subscribe to the MassRobotics Newsletter
Learn about our residents and partners, participate in our events and challenges, and receive robotics and AI industry news.